Industrial Man Lifts brings you this warehouse racking system guide is intended to provide you with useful information which will help you discover how to choose or upgrade local systems.
If you have a customized racking system already installed, then some of the details included here may still be available for your system.
That allows you to be able to use your racking system more effectively, while improving the safety profile of your system.
4 Types of Racking Systems
There are four basic types of racking systems that can be used within your warehouse right now. Each type has core strengths and weaknesses that must be considered, based on the requirements of your facility.
-
Option #1: Selective Racks
This warehouse racking system provides you with complete access to all your pallets. That availability comes at the expense of a lower overall storage density. You’ll need an aisle for every row with this type of system. In return, you’ll be able to move pallets around your facility faster and store items quickly and safely.
-
Option #2: Drive-In Racks
This type of system requires a first-in, last-out approach. It is a system which reduces your overall selectivity, while improving the product density on your floor. This is the type of racking system to use if you require longer storage life without immediate access to items. These systems are most-often found in cold-storage warehouse applications.
-
Option #3: Pushback Systems
This is another first-in, last-out racking system approach. The benefit of this system is that you have improved selectivity, as it allows for a different SKU for each level. You’ll be required to have an angled pitch with this type of system and it demands consistent levels of vertical space.
-
Option #4: Pallet Flow
This is a first-in, first-out system. It offers the best levels of storage density, while having the least amount of selectivity. As an added benefit, there are usually fewer handling costs associated with this type of warehouse racking system. Just two aisles are necessary for this system option, which means you can reduce your passageway spacing by up to 75%. That equates to fewer forklifts in operation, fewer fuel costs, and a similar handling capability.
Accessories for Warehouse Racking Systems
Warehouse racking systems are designed to be fully functional on their own once installed. To customize the experience, however, there are some features which can be added to a system to add flexibility or make it more productive.
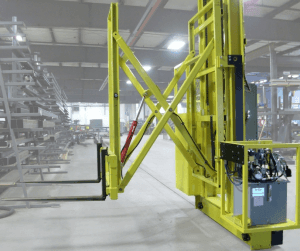
Here are some of the top accessory options to consider if you’re thinking about the installation of a racking system today.
-
Column Protectors
This feature will protect your racking system against a collision impact from a forklift. There are several material types available, from poly to steel, to meet the specific needs you may have.
-
Frame Spacers
These small inserts help to make your rows and overhang with your rack more uniform. Depending upon the height of your racking system, you may require 2-3 spacers per frame for best results.
-
Mesh Panels
You can improve the security of your facility by installing mesh panels around your racking system. They will also reduce product spills. You can include safety enclosures, such as a locked gate, with the panels too.
-
Pallet Supports
When inserted into your racking system, this feature will support a pallet which is not deep enough to be supported by the depth of a standard rack frame.
-
Safety Netting
This feature reduces the number of pallet falls that may be experienced on the warehouse floor. You can configure the netting to work with the pallet weight and fall trajectories which are unique to your facility.
-
Safety Straps
These straps function in manner that is similar to netting to prevent accidents. Most straps install on current warehouse racking systems and require no tools for placement.
-
Wire Decks
Decking on your racking system will give you better stability when placing pallets. You’ll still receive good ventilation for your pallets. This feature will increase the support your racking system provides as well.
You also have an option to convert some racks into gravity-flow storage when smaller inventory items need to be stored and orders picked. Roller shelves, knuckle-overs, and extended lanes are potential possibilities.
How to Configure Your Selective Racks
- You must first determine the depth, width, height, and weight of the largest load/pallet which must be stored. You’ll need to measure the load you must store. If the load is smaller than the pallet on any measurement, then use the pallet measurement instead of the load measurement.
- For your height measurement, remember to include the height of the pallet.
- To determine your rack depth for your uprights, remove 6 inches from your pallet depth. A standard 48-inch pallet would give you a 42-inch rack depth measurement.
- Then measure your width and capacity. Based on having two pallets placed on each beam, you can double your load width, then add 12 inches to your measurement. Using the standard pallet with the rack depth measurement, you’d have a final beam length measurement of 96 inches (42 x 2 + 12).
- You must ensure that your beam capacity can carry the weight of the load you intend to store.
- When determining your final pallet height, remember to multiply the number of pallets stored, less one, to determine your overall storage and clearance availability.
Why a Warehouse Racking System is Necessary
If you are storing products, then a racking system will give you aisles to manage instead of piles of pallets. Your inventory management because faster, easier, and safer with a racking system as well.
There are many variables to consider when attempting to select a warehouse racking system. The amount of inventory you manage, the speed of your deliveries, and the spatial aspects of your warehouse will help to determine the type of racking system you require.
Always take the safety of your floor seriously. Whether you choose to incorporate specific safety features or implement policies on your own, being proactive about safety will prevent many accidents from occurring.
Review OSHA guidelines for warehouse racking systems to ensure local compliance will all current regulations.